作者:金榮植 來(lái)源:《金屬加工(熱加工)》雜志 輪的整個(gè)輪廓需要淬火以獲得必須的抗麻點(diǎn)、耐磨以及疲勞強(qiáng)度、較小的畸變。而這樣的淬火輪廓很難通過(guò)常規(guī)感應(yīng)淬火方法獲得,對(duì)此可以采用雙頻感應(yīng)淬火、同步雙頻感應(yīng)淬火等,能夠得到沿齒廓均勻分布的淬硬層。同時(shí),由于加熱速度快、時(shí)間短,因此節(jié)能效果顯著。 今天作者拋磚引玉,簡(jiǎn)單的聊聊比較先進(jìn)的齒輪感應(yīng)熱處理技術(shù),不足之處大家可以補(bǔ)充。美國(guó)GM公司是最早應(yīng)用齒輪感應(yīng)淬火代替滲碳淬火的企業(yè)之一。齒輪感應(yīng)淬火取代滲碳淬火的主要優(yōu)點(diǎn)是周期短、能耗低、畸變小。
一、齒輪雙頻感應(yīng)淬火技術(shù) 常規(guī)(傳統(tǒng))雙頻感應(yīng)淬火是兩種頻率的電源分別施加到兩個(gè)感應(yīng)器,齒輪需要從低頻感應(yīng)器預(yù)熱之后快速移到另一高頻感應(yīng)器加熱并進(jìn)行淬火,見(jiàn)圖1。雙頻感應(yīng)淬火是采用低頻加熱向里進(jìn)行熱能量的擴(kuò)散,最后高頻加熱向表層,即“低頻趨里,高頻趨表”的特征。
圖1 常規(guī)的齒輪雙頻淬火示意 雙頻感應(yīng)淬火是增加淬硬層深度并使硬度分布更為合理的感應(yīng)加熱淬火方法。即用中頻-高頻依次加熱方法可獲得沿齒廓分布的硬化層,而且齒輪熱處理畸變小。例如,模數(shù)為4mm的齒輪先用中頻電流加熱(2.5~3s)齒溝和接近齒根的齒側(cè),然后再用250kHz高頻電流加熱(0.6~0.7s)齒頂和接近齒頂?shù)凝X側(cè),然后淬火。東風(fēng)汽車集團(tuán)公司對(duì)材料為45鋼、模數(shù)為3的齒輪進(jìn)行雙頻感應(yīng)加熱淬火時(shí),能夠得到沿齒輪廓均勻分布的淬硬層,淬硬層為0.8mm時(shí),具有最佳彎曲疲勞性能,與SCM420(相當(dāng)于20CrMo鋼)滲碳齒輪疲勞性能基本相當(dāng),疲勞極限可以達(dá)到1450MPa。日本電氣興業(yè)公司通過(guò)對(duì)齒輪雙頻淬火法進(jìn)行試驗(yàn),可得到比齒輪單頻淬火法和滲碳淬火法小的畸變,漸開線圓柱齒輪(見(jiàn)圖2),模數(shù)2mm,全齒高4.7mm,齒數(shù)36,材料為S45C鋼(相當(dāng)于45鋼)。齒面經(jīng)剃齒精加工,預(yù)備熱處理為調(diào)質(zhì)。
圖2 試驗(yàn)齒輪形狀 雙頻感應(yīng)淬火方法如圖6所示。首先把齒輪放在夾具上,然后隨中心軸高速旋轉(zhuǎn),同時(shí)由中頻電源送入f=3000Hz的電流,進(jìn)入感應(yīng)器(A),對(duì)全齒形(齒頂、齒面、齒根)進(jìn)行預(yù)熱。當(dāng)齒輪達(dá)到最佳溫度時(shí),中頻電源斷電,齒輪迅速降到淬火加熱的感應(yīng)器(B)中,同時(shí)高頻電源開始送電,頻率f=140kHz,對(duì)齒輪的齒面和齒頂進(jìn)行快速的淬火加熱,待齒面達(dá)到淬火溫度時(shí),切斷高頻電源,降低齒輪的旋轉(zhuǎn)速度,同時(shí)淬火用水套中噴出冷卻水,使齒面、齒頂、齒根迅速冷卻,獲得沿齒形分布的硬化層。
圖3 雙頻感應(yīng)淬火方法 1. 噴水孔2. 齒輪3. 預(yù)熱用感應(yīng)器(A) 4. 高頻加熱感應(yīng)器(B)+淬火用水套5. 夾具 表1為齒輪(見(jiàn)圖2)三種熱處理工藝參數(shù)。表1 雙頻、單頻淬火及滲碳淬火的主要工藝參數(shù)  三種工藝處理后的齒輪畸變、殘留壓應(yīng)力及沿齒廓仿形率的檢測(cè)結(jié)果見(jiàn)表2。通過(guò)表2可知,雙頻淬火后的齒輪熱處理畸變最小,精度最高,殘留壓應(yīng)力最高。表2 滲碳淬火、單頻感應(yīng)淬火及雙頻感應(yīng)淬火后的熱畸變結(jié)果 

二、齒輪的同步雙頻感應(yīng)淬火技術(shù)(SDF法) 現(xiàn)代化的雙頻感應(yīng)淬火技術(shù)是在一個(gè)感應(yīng)圈上同時(shí)輸出高頻(如200~400kHz)和中頻(如10~15kHz)兩種不同頻率對(duì)一個(gè)工件進(jìn)行快速熱處理,即同步雙頻感應(yīng)淬火(見(jiàn)圖4)。
圖4 現(xiàn)代化齒輪同步雙頻淬火示意 如SDF發(fā)生器包括正常功率輸出的一個(gè)HF(高頻)和一個(gè)MF(中頻)采用IGBT技術(shù),在中頻振蕩基礎(chǔ)上疊加高頻振蕩。HF和MF功率元件能夠從2%~100%進(jìn)行連續(xù)調(diào)整,采用集成PLC控制,具有多個(gè)程序時(shí)間和功率設(shè)定,特別適合處理類似齒輪等復(fù)雜表面的工件。如SDF同步雙頻感應(yīng)淬火可獲得沿齒廓分布的硬化層,可代替部分滲碳淬火工藝,如因錐齒輪齒頂形狀很復(fù)雜,在滲碳淬火后非常不容易進(jìn)行磨齒以校正其畸變,而采用SDF同步雙頻感應(yīng)淬火處理時(shí)間[加熱時(shí)間200ms,功率580kW(MF+HF),10kHz和230kHz]與傳統(tǒng)滲碳淬火相比,僅為40%左右,加上感應(yīng)熱處理為表面局部加熱淬火,因此熱處理畸變很小,完全可以達(dá)到畸變公差要求,齒輪不需磨齒。目前,SDF同步雙頻感應(yīng)加熱設(shè)備功率達(dá)到3MW以上,完全可以滿足大中型齒輪的表面熱處理需求。圖5為同步雙頻感應(yīng)淬火的幾種齒輪仿形硬化層分布。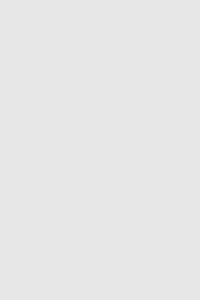
圖5 同步雙頻感應(yīng)淬火的幾種齒輪仿形硬化層分布 ①同步雙頻感應(yīng)加熱,沿齒廓加熱,可實(shí)現(xiàn)齒根和齒頂?shù)耐瑫r(shí)受熱,熱量可集中在工件的輪廓表面,從而獲得均勻的齒廓硬化層,硬化層深度根據(jù)需要快速調(diào)節(jié)。②具有快速、位置精確硬化、能耗節(jié)約50%、熱處理后畸變小、產(chǎn)能高及使用成本低等一系列優(yōu)點(diǎn)。③易于集成在現(xiàn)有機(jī)械加工生產(chǎn)線上。(3)齒輪感應(yīng)淬火加工的全自動(dòng)化德國(guó)eldec公司與德國(guó)EMA公司合作開發(fā)的拾取式的齒輪感應(yīng)淬火機(jī)床(拾取式,即工裝在固定的位置上,齒輪是移動(dòng)的,由機(jī)械手抓取并進(jìn)行淬火),最終實(shí)現(xiàn)了齒輪感應(yīng)淬火加工的全自動(dòng)化。由于能夠準(zhǔn)確地知道工件在加工過(guò)程中能量和畸變量的變化情況,能量控制的精度可達(dá)到±2%,并且有準(zhǔn)確的記錄,而這在滲碳爐中是做不到的。SDF感應(yīng)加熱設(shè)備與技術(shù)還可以用于錐齒輪、從動(dòng)行星輪、蝸桿、齒條等感應(yīng)淬火。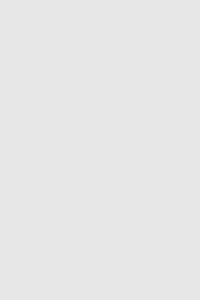
三、感應(yīng)加熱氣體滲碳技術(shù) 利用高頻感應(yīng)加熱直流放電進(jìn)行滲碳,可獲得0.35~0.45mm滲碳層,滲層表面碳含量0.9%~1.05%(質(zhì)量分?jǐn)?shù))。與常規(guī)氣體滲碳相比,高頻加熱氣體滲碳技術(shù)可縮短生產(chǎn)周期至原來(lái)的1/10~1/2,因此節(jié)能效果顯著。在如圖6所示的中頻感應(yīng)加熱裝置中,將工件(齒輪)以2000~8000Hz(50kW)中頻電流加熱到1050~1080℃,同時(shí)通入滲碳?xì)怏w(例如,天然氣與吸熱式氣氛的混合氣)。滲碳過(guò)程持續(xù)40~45min,可以得到0.8~1.2mm的滲碳層。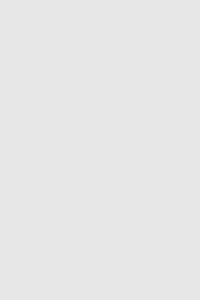
圖6 感應(yīng)加熱氣體滲碳裝置示意 1.油槽2.油缸3.感應(yīng)圈4.齒輪 在上述裝置中,每1.5~3min可推出一個(gè)滲碳后的齒輪,經(jīng)預(yù)冷至820~870℃,然后進(jìn)行淬火。常規(guī)氣體滲碳時(shí),要獲得0.8~1.2mm滲碳層深度,需要滲碳時(shí)間5~6h。與常規(guī)氣體滲碳相比,采用感應(yīng)加熱氣體滲碳,可縮短滲碳周期80%以上,因此該工藝節(jié)能降耗效果十分顯著。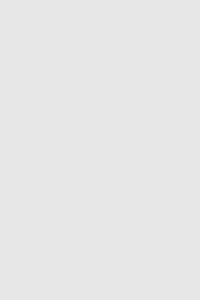
四、新的模壓式感應(yīng)淬火技術(shù) 目前,國(guó)外(如德國(guó)EMA感應(yīng)科技開發(fā)公司)開發(fā)了一種模壓式感應(yīng)淬火技術(shù),其綜合了感應(yīng)淬火和壓床淬火工藝的優(yōu)點(diǎn),其工藝路線是,齒輪感應(yīng)淬火后直接采用模具淬火,然后進(jìn)行原位感應(yīng)加熱回火。其主要裝備是具有模壓式淬火裝置以及感應(yīng)加熱系統(tǒng)的新型淬火機(jī)床。其適用于高精度圓環(huán)形工件的批量生產(chǎn),如齒圈、錐齒輪和同步器齒套等的淬火。該工藝不僅適合于中碳鋼的直接壓床淬火,也適合于滲碳后的齒輪壓床淬火。例如,滲碳后變形的錐齒輪,材料為16MnCrS5鋼,要求淬火處理。(1)模壓式感應(yīng)淬火工藝參數(shù)16MnCrS5鋼錐齒輪模壓式感應(yīng)淬火工藝參數(shù)及檢驗(yàn)結(jié)果如表3所示。表3 錐齒輪模壓式感應(yīng)淬火工藝參數(shù)及檢驗(yàn)結(jié)果 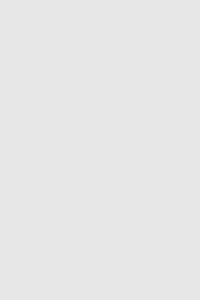 (2)模壓式感應(yīng)淬火工藝過(guò)程圖7為錐齒輪模壓感應(yīng)淬火示意,首先將滲碳后的錐齒輪固定到非導(dǎo)磁性的定心和夾持裝置上(步驟1),通過(guò)電磁感應(yīng)(線圈)將齒輪加熱到約900℃(步驟2)。保溫一定時(shí)間后,齒輪達(dá)到一個(gè)相同或均勻的溫度,芯軸、壓模到位(步驟3),壓模施壓狀態(tài)下立即用淬火冷卻介質(zhì)噴淋齒輪(步驟4)。校正芯軸可以有效地防止齒輪收縮。在步驟4淬火結(jié)束后,不再需要壓模,直接進(jìn)入感應(yīng)回火階段。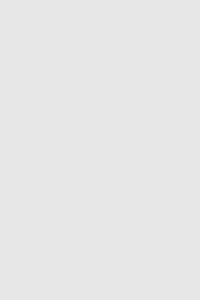
圖7 錐齒輪模壓式感應(yīng)淬火示意 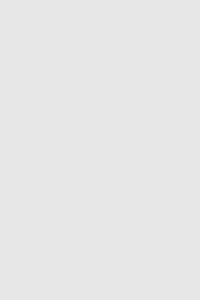
五、模壓式感應(yīng)淬回火生產(chǎn)線 模壓式感應(yīng)淬火+回火生產(chǎn)線如圖8所示,其只有轉(zhuǎn)底滲碳爐和感應(yīng)壓淬機(jī)床。感應(yīng)淬火采用水溶性淬火冷卻介質(zhì),熱處理后的齒輪不需要清洗,同時(shí)可去掉專門配備的回火爐。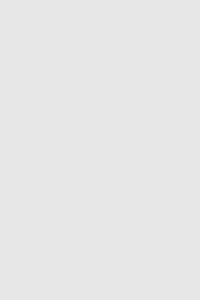
圖8 齒輪模壓式感應(yīng)淬火回火生產(chǎn)線 1. 上下料機(jī)構(gòu)2. 轉(zhuǎn)底式滲碳爐3. 轉(zhuǎn)移機(jī)構(gòu) 4. 感應(yīng)模壓淬火回火機(jī)床
|