技術(shù)變化對(duì)電池互連工藝和組件整體結(jié)構(gòu)產(chǎn)生了深遠(yuǎn)的影響,從以下幾個(gè)例子可見一斑:新的電池金屬化設(shè)計(jì)和技術(shù)提高了電池效率,而組件互連設(shè)計(jì)的革新--例如半切電池--可以通過降低電池到組件(cell-to-module:CTM)損失來提高組件輸出功率。而設(shè)備供應(yīng)商們正在提供新的生產(chǎn)線,將最先進(jìn)的三主柵電池設(shè)計(jì)提升至四甚至是五主柵。 本文將要介紹的由SCHMID集團(tuán)研發(fā)的多主柵(multi-busbar:MBB)技術(shù)是經(jīng)過進(jìn)一步優(yōu)化的太陽能電池互連概念。串焊工藝中,該技術(shù)采用15Cu線將相鄰電池的前表面和背面交替連接起來,完成電池-電池互連。本文對(duì)相關(guān)設(shè)備和互連工藝進(jìn)行了討論,并利用微結(jié)構(gòu)表征技術(shù)來探究電極結(jié)構(gòu)和它的可靠性。 本文所推薦的技術(shù)都是以減少電池前端電極銀(Ag)材料的消耗量為目標(biāo)的。通過多主柵設(shè)計(jì),由于互連電池串的總串聯(lián)電阻得到降低、柵線面積大幅減小而增加了光照利用率,組件性能因此得到有效提高。 使用光伏電池和組件MBB技術(shù)的4個(gè)主要好處在于:1降低各種類型電池的單塊電池銀材料使用量。2通過采用新的電池金屬化結(jié)構(gòu)和多主柵焊接設(shè)計(jì)提高電池和組件效率。3通過設(shè)備革新,可以改裝現(xiàn)有組件生產(chǎn)線、可靠的串焊工藝、傳統(tǒng)電池串疊層和組件層壓。4提高組件可靠性和降低熱應(yīng)力引起的壓力和電池碎裂概率。  本文展望了電池技術(shù)的發(fā)展前景,綜合概述了多主柵互連工藝以及組件整體產(chǎn)生工藝。與此同時(shí),本文還介紹了小型化焊點(diǎn)的微觀力學(xué)和微結(jié)構(gòu)分析。最后部分將會(huì)側(cè)重于多主柵互連技術(shù)的力學(xué)性能和可靠性優(yōu)勢(shì)。
2010年,光伏行業(yè)消耗了全球每年Ag材料供應(yīng)量的7%[7]。而在Ag使用量增加的同時(shí),Ag價(jià)格也水漲船高:這嚴(yán)重制約了太陽能電池行業(yè)實(shí)現(xiàn)產(chǎn)能提高和成本下降兩者并舉的發(fā)展。因此,如今光伏工業(yè)的主要目標(biāo)之一是降低太陽能電池生產(chǎn)的Ag使用量。 研究結(jié)果表明,多主柵設(shè)計(jì)比最新三主柵電池設(shè)計(jì)能獲得更高的電池和組件效率。研究人員對(duì)多主柵設(shè)計(jì)進(jìn)行了優(yōu)化,從而減小遮蔭面積和Ag消耗量。本文提出的柵線布局是基于小型焊盤和網(wǎng)柵設(shè)計(jì),以替代將連續(xù)主柵作為銅帶焊盤的傳統(tǒng)概念。此外研發(fā)人員還開發(fā)了新的測(cè)試和表征程序。 在傳統(tǒng)三主柵布局中,主柵之間的子?xùn)砰L(zhǎng)度以及相關(guān)電阻損失限制了子?xùn)艑挾鹊倪M(jìn)一步減小,并因此決定了獲得有效填充因子所需的Ag消耗量。而多主柵設(shè)計(jì)則縮短了子?xùn)砰L(zhǎng)度,從而能充分挖掘現(xiàn)代金屬化技術(shù)的潛能,例如細(xì)線網(wǎng)印以及結(jié)合了光誘導(dǎo)鍍的噴墨種子層印刷技術(shù)。多主柵結(jié)構(gòu)的主要優(yōu)勢(shì)在于高填充因子,以及大幅降低的Ag消耗量以及較低的活性區(qū)域遮蔭面積。 

太陽能電池金屬化使用兩種不同的工藝:1)細(xì)線絲網(wǎng)印刷,以及2)結(jié)合電鍍技術(shù)的前端電極種子層印刷。表一對(duì)比了多主柵和三主柵的Ag消耗量。通過提高對(duì)準(zhǔn)精度、減小線寬和使用雙層印刷,絲網(wǎng)印刷工藝正得到逐步優(yōu)化,而印刷漿料消耗在過去幾年也大幅降低:實(shí)現(xiàn)了40%的降幅。而其它方法,例如種子層噴墨印刷和Ag電鍍,只需消耗三分之一的Ag材料。這一結(jié)果證明了太陽能電池有效前端電極結(jié)構(gòu)可以進(jìn)一步降低Ag使用量。 前表面金屬化設(shè)計(jì)是非常靈活的。金屬電極的圖案可以進(jìn)行自由修改以配合特定客戶所要求的布局、工藝要求(例如焊盤尺寸和對(duì)準(zhǔn)精度之間的權(quán)衡,等)和優(yōu)化電池效率。圖一和圖二顯示了兩種不同的金屬化圖案:1)由種子層 噴墨印刷和電鍍工藝制得,并采用標(biāo)準(zhǔn)的少主柵布局;2)經(jīng)過優(yōu)化設(shè)計(jì)的絲網(wǎng)印刷電極,進(jìn)一步減少焊盤數(shù)量。研究結(jié)果顯示Ag消耗量被大幅度減少;不僅如此,多主柵概念測(cè)符合國(guó)際路線圖所提到的長(zhǎng)期目標(biāo):“國(guó)際光伏技術(shù)路線圖”(ITRVP)指出了2020年每塊電池Ag消耗量減少至50mg的目標(biāo)。 細(xì)銅線多主柵電池互連概念最初由加拿大公司Day4Energy提出;該技術(shù)如今由梅耶博格公司以“智能柵線連接”概念推向市場(chǎng)。智能柵線方法將串焊和層壓工藝集成到單個(gè)步驟中,即用覆銦電線連接太陽能電池。與之相比,本文討論的多主柵連接概念與經(jīng)典串焊步驟相似,也是在電極制作完成后才進(jìn)行標(biāo)準(zhǔn)層壓工藝:太陽能電池依然以交替方式互連,從一塊電池的前表面到相鄰電池的背表面。電池之間通過15Cu線進(jìn)行機(jī)械和電互連,隨后組合成傳統(tǒng)電池串;緊接著將其抓起并移動(dòng)至其它地方,以準(zhǔn)備進(jìn)一步組件封裝(交互連接和封裝層壓)。采用這種方法的優(yōu)點(diǎn)在于所有的技術(shù)進(jìn)展能直接集成到現(xiàn)有生產(chǎn)線中:唯一要做的只是更換串焊設(shè)備。 隨著電池層面多主柵技術(shù)的發(fā)展,需要新一代電池-電池互連工藝設(shè)備來滿足少主柵電池對(duì)連接細(xì)小Cu線的需求。由于電池和柵線的對(duì)準(zhǔn)非常重要,所以多主柵串焊機(jī)使用高精確度圖像處理技術(shù)來計(jì)算金屬化圖案的位置。隨后,電池串被放置在通過IR焊錫預(yù)加熱的真空腔中進(jìn)行焊接(見圖三)。所有覆銦15Cu線在都一步之內(nèi)焊在電池前表面和背表面,如圖四所示。為了能輕松安裝組件陣列,電池串兩端15Cu線是自動(dòng)通過焊帶末端的。圖五顯示了Cu線逐點(diǎn)焊接在多主柵電池金屬電極上的SEM圖。 

如上所述,總的組件封裝過程采用了最新的工作流程。金屬化工藝、電池檢測(cè)和測(cè)量,以及串焊工藝設(shè)備都會(huì)受到技術(shù)變化的影響,但后續(xù)電池串與接線盒互連以及組件層壓則依然是采用現(xiàn)有標(biāo)準(zhǔn)工藝。 

圖六顯示多主柵組件制造概念的工藝流程圖。相比于現(xiàn)有傳統(tǒng)光伏電池和組件封裝工藝,該技術(shù)不需要多余的步驟就能實(shí)現(xiàn)主柵電池/組件封裝。在電池制造層面,只有金屬化工藝才經(jīng)過了修改:絲網(wǎng)印刷工藝依然被使用到,但需要新的網(wǎng)版。在控制質(zhì)量和產(chǎn)品檢測(cè)方面,由于多主柵電池前表面布局經(jīng)過重新設(shè)計(jì),所以需要新的電極連接裝置。 在進(jìn)行組件生產(chǎn)時(shí),由于只需要重新安裝串焊設(shè)備,所以可以輕松實(shí)現(xiàn)增產(chǎn)。在進(jìn)行疊層操作時(shí),電池串被放置在玻璃上面。此外,用多主柵15Cu線交聯(lián)進(jìn)行電池串互連時(shí),不需要對(duì)現(xiàn)有工藝進(jìn)行大幅修改。 電極結(jié)構(gòu)和焊點(diǎn)的評(píng)估 除了電池層面外,我們還進(jìn)行了與電極形式、工藝和材料互連相關(guān)的擴(kuò)展研究,以優(yōu)化和證實(shí)這種組件概念。最近,Schindler等人對(duì)焊接工藝后的MBB電池電極結(jié)構(gòu)進(jìn)行了研究。通過采用微力學(xué)測(cè)試,作者對(duì)不同技術(shù)路線進(jìn)行了評(píng)估,例如改變Cu線半徑或電池金屬。 

通過借鑒微電子和微系統(tǒng)技術(shù)的故障診斷經(jīng)驗(yàn),以及粘附技術(shù)的材料評(píng)估和系統(tǒng)集成(例如線結(jié)合電極或焊接電極),人們共同開發(fā)了一款通用的設(shè)備(見圖七)用于表征太陽能電池互連(包括標(biāo)準(zhǔn)H圖形電池布局和新電池金屬化概念和圖案)。MBB焊接點(diǎn)的力學(xué)測(cè)試是通過小型化焊接點(diǎn)拉力測(cè)試進(jìn)行評(píng)估的,因?yàn)檫@是一種測(cè)試工藝參數(shù)和材料共同對(duì)互連影響的合適方法。焊盤的表征是在太陽能電池前表面金屬完成的(如圖八)。測(cè)試序列中單點(diǎn)拉力互連值屬于最大值,隨后計(jì)算所測(cè)試樣品的平均值和標(biāo)準(zhǔn)偏差。隨后,拉力測(cè)試之后的斷裂模型被記錄下來,以尋找測(cè)試方法中力的大小與應(yīng)力引入電極衰退之間的潛在關(guān)系。這種測(cè)試表明了這些小型化電極的優(yōu)異應(yīng)力值。測(cè)試結(jié)果還可以看出,金屬化工藝在焊點(diǎn)拉力測(cè)試中的機(jī)械應(yīng)力起到了重要作用。 噴墨種子層印刷和鍍Ag焊接結(jié)構(gòu)上焊點(diǎn)的拉力值比絲網(wǎng)印刷低。對(duì)于絲網(wǎng)印刷電極盤,拉力值超過了1牛,而有幾條電極的測(cè)量值超過了2.5牛(圖九)。在力學(xué)測(cè)試中,采用噴墨種子層印刷和鍍Ag技術(shù)的焊點(diǎn)形成的拉力平均值為1牛。為了比較多主柵焊點(diǎn)和標(biāo)準(zhǔn)焊帶的脫落應(yīng)力值,需要考慮焊接區(qū)域的寬度。大約600微米電極區(qū)域?qū)挾仁堑湫腿鳀藕笌挾?1.5毫米)的40%。 
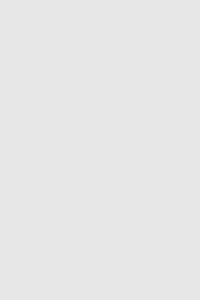
在改變Cu電線直徑時(shí)沒有觀察到明顯的焊接電極質(zhì)量差異(圖十):在用生產(chǎn)設(shè)備焊接時(shí),兩種不同直徑電線的測(cè)試結(jié)果相似。 在拉力測(cè)試后對(duì)碎片樣式的詳細(xì)分析顯示兩種金屬化類型有相當(dāng)大的不同(圖十一)。柵線直徑變化對(duì)拉力測(cè)試之后的碎片樣式?jīng)]有明顯的影響。 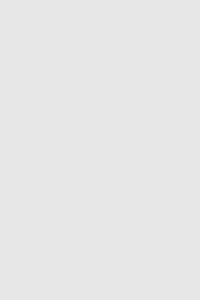 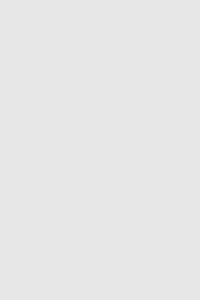 絲網(wǎng)印刷工藝得到的焊盤顯示明顯的焊接彎月面電極殘余和側(cè)壁焊接殘余。而噴墨種子層印刷和鍍Ag盤結(jié)構(gòu)在測(cè)試之后則完全與電池片分離,并且可以看到電池表面結(jié)構(gòu)。此外還在樣品中發(fā)現(xiàn)了焊接區(qū)域內(nèi)的部分硅碎片。兩種金屬電極類型都發(fā)現(xiàn)了貝殼狀的碎片(如圖十二),但不能和特定應(yīng)力值相聯(lián)系。
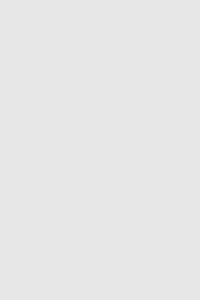
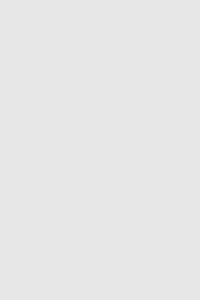
焊接點(diǎn)的電極結(jié)構(gòu)則通過微結(jié)構(gòu)測(cè)試來分析。SEM圖(圖十三)證明串焊設(shè)備的焊接結(jié)果非常統(tǒng)一。Cu線的錫包覆總是和金屬盤區(qū)域糾纏,可以看到統(tǒng)一的Cu線新月。圖十四中的金相學(xué)截面詳細(xì)顯示焊接點(diǎn)的新月。焊接新月從Cu線到焊盤區(qū)域凝固成為統(tǒng)一形狀,沒有檢測(cè)到Ag金屬化的反浸潤(rùn)或溶解。而焊點(diǎn)體積則明顯大于傳統(tǒng)覆錫銅焊帶互連焊接點(diǎn);從應(yīng)力釋放和材料科學(xué)角度看,這一特性將會(huì)成為電極可靠性的額外優(yōu)勢(shì),也是對(duì)總組件性能和可靠性的額外優(yōu)勢(shì)。
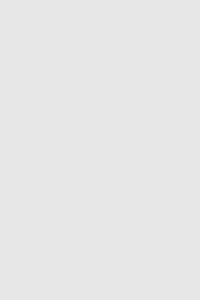
新的金屬化布局證明了高效率電池的特性不會(huì)隨著前端電池電極Ag使用量的減少而變化。兩種技術(shù)方法--細(xì)線絲網(wǎng)印刷和種子層噴墨結(jié)合光誘導(dǎo)鍍--使得新的電池金屬化布局能大幅減小子?xùn)艑挾群徒孛妗?br> 對(duì)于電池金屬化和電線類型來說,逐點(diǎn)串焊工藝得到了可靠的焊接電極。我們將會(huì)推出進(jìn)一步的研究來判定所有設(shè)備裝置在穩(wěn)定性和可重復(fù)焊接參數(shù)方面的性能。 焊點(diǎn)的微力學(xué)測(cè)試是通過拉力測(cè)試方法進(jìn)行的,是檢測(cè)電極焊點(diǎn)力學(xué)性能的有效方法。拉力測(cè)試特別是絲網(wǎng)印刷MBB結(jié)構(gòu),產(chǎn)生好的最小化焊接應(yīng)力:這項(xiàng)值可以和三主柵的相提并論甚至好于后者。金屬化工藝在測(cè)試時(shí)對(duì)焊點(diǎn)的力學(xué)性能起到很大作用。鍍銀結(jié)構(gòu)的焊點(diǎn)展現(xiàn)比Ag金屬絲網(wǎng)印刷更低拉力。對(duì)于絲網(wǎng)印刷電極,拉力大于1牛,有些電極甚至超過2.5牛。噴墨種子層印刷和光誘導(dǎo)鍍Ag技術(shù)的焊點(diǎn)在應(yīng)力測(cè)試中產(chǎn)生平均值為1牛的應(yīng)力。所有電極結(jié)構(gòu)都顯示了非常好的Cu線到焊接區(qū)域的浸潤(rùn)性。多主柵連接設(shè)備在焊盤區(qū)域形成了統(tǒng)一的焊接半月。所測(cè)試的拉力并不決定于Cu線直徑(250微米vs300微米),但對(duì)于減少遮陰或降低串聯(lián)電阻是有意義的。測(cè)量最小拉力這一仍與組件可靠性相關(guān)的參數(shù)將是進(jìn)一步測(cè)試的主要關(guān)注點(diǎn)。顯然,不同金屬化技術(shù)將會(huì)顯示不同的最小拉力。 對(duì)電池碎裂和引入應(yīng)力對(duì)焊接的影響進(jìn)一步測(cè)試正在持續(xù)當(dāng)中。結(jié)合了實(shí)時(shí)電致發(fā)光(EL)和四點(diǎn)彎曲裝置的測(cè)試,以評(píng)估工藝參數(shù)、組件布局和所用材料對(duì)電池碎裂的影響。 據(jù)推測(cè),多主柵金屬化結(jié)構(gòu)將減少電池機(jī)械引入應(yīng)力:電池碎裂的可能性也因此降低。對(duì)焊點(diǎn)的機(jī)械應(yīng)力也將提高,但由于焊接體積大得多,釋放應(yīng)力的潛能也增加。進(jìn)一步的測(cè)試正在進(jìn)行中,并將會(huì)成為下次文章的主題,以證明多主柵組件技術(shù)的好處和可靠性。
Sebastian Schindler, Fraunhofer CSP, Halle, & Michael Volk, SCHMID Group, Freudenstadt, Germany
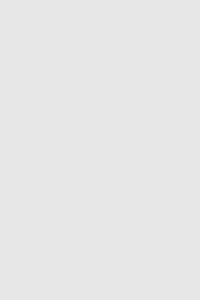 1.組串式逆變器的歷史及認(rèn)識(shí)的誤區(qū)
2.PID 效應(yīng)及影響因素 3.數(shù)據(jù)告訴你,背接觸組件的抗功率衰減情況是喜是憂? 4.N型高效單晶光伏電池技術(shù)發(fā)展現(xiàn)狀及產(chǎn)業(yè)化前景
|